Impact of Risk-Based Inspection in Oil and Gas Industry
- March 30, 2022
- Posted by: Velosi Author
- Categories: Asset Integrity, Insights
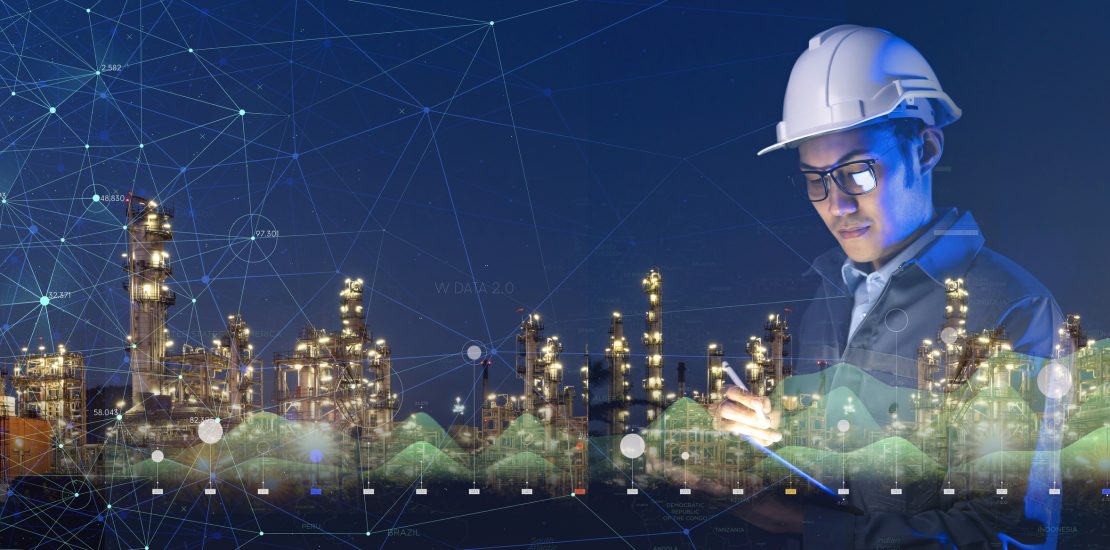
Impact of Risk-Based Inspection in Oil and Gas Industry
What is Risk-Based Inspection?
RBI is an inspection methodology for identifying and managing mechanical integrity in static equipment and pipes, but it is often used in isolation as part of a reliability program that ignores details. Moving away from time-based inspections and toward risk-based inspections has benefited the oil and gas sector, although marginally. However, the expenses of developing and executing an RBI strategy are debatable. RBI is seen by the industry as a pathway to gain economic benefits from longer run lengths and to make better use of inspection resources by automated NDT or non-invasive inspection schemes. Regulatory pressure will ensure that the RBI process is rigorously followed, ensuring that inspection decisions are based on adequate information and expertise.
Failure Analysis
Nearly two-thirds of the failure costs in the refining industry are due to fixed equipment failures. Companies lose staggering sums of money as a result of failure that could have been avoided.
The average refinery has a risk of $25 million per year due to the failures of fixed equipment. Effective inspection and maintenance programs can help to reduce equipment and structural failures. The scope, method, timing, and acceptance criteria of inspection/maintenance can all have a significant impact on the likelihood of component failure. The majority of today’s in-service inspection and maintenance requirements are based on prior experience and engineering judgment. At best, some include an implicit risk assessment (probability of failure times consequence). Effective inspection and maintenance programs can help to reduce equipment and structural failures. The scope, method, timing, and acceptance criteria of inspection/maintenance can all have a significant impact on the likelihood of component failure. The majority of today’s in-service inspection and maintenance requirements are based on prior experience and engineering judgment. Some, at best, include an implicit
Velosi has been providing and implementing RBI for various clients for four decades. Every RBI assessment they have performed has endeavoured to find an inspection plan that can address risk at the equipment or component level. The plans highlight risk from a safety, health, environmental, and/or economic standpoint.
How does the RBI strategy work?
Although the benefits of Risk-Based methods for inspection and repair or replacement are recognized by different industry sectors to gain the full advantage, the approach must overcome some challenges.
- Basic approaches for data collection for RBI –RBI informs the inspection judgment on where, when, and how to inspect most equipment; the technology is effective in assets that have a corrosive service that results in severe damage mechanisms but around 80% of the processing plant equipment are not susceptible to high corrosion rate and thus implementing an RBI program with all necessary inspection activities is simply ‘overkill’.
- Velosi has a strategy for developing optimized, cost-effective inspection and maintenance programs within the context of asset and risk management. The strategy integrates reliability and risk assessments with data derived from expert judgment, physical models, and plant-specific and generic data. This assessment distinguishes critical components from non-critical components, assisting companies globally in determining where special maintenance measures are required. Our extensive qualitative and quantitative techniques are based on internationally accepted standards and guidelines, and we then tailor the solutions to your specific concerns.
What are some of the benefits of Risk-based Inception?
There are some of the benefits of RBI such as;
- Optimizing risk management via frequent risk analysis and mitigation keeping downtime to a minimum by avoiding major failures
- Saving money through the implementation of a far more effective Inspection strategy and the reduction of unscheduled outages
- Optimum use of labour resources via the elimination of needless inspections
Why do Companies commit to such a program?
Any accident that has occurred in the past may define the current health and safety policies. Or the inspection costs are too high and the overall budget needs to be cut. Or there are too many unplanned shutdowns after leaks or releases. The RBI has worked with the majority of clients to optimize inspection intervals. Sometimes, the user implements an RBI program to improve the overall reliability of equipment assets.
Some of the challenges associated with the implementation of RBI are knowledge, skills, and resources. Mostly, the organizations that are performing RBI do not have the requisite knowledge of the RBI process and they lack skilled people to sustain the program. The individuals responsible for implementing the project are typically engaged in other work and to sustain the program, the project needs to be prioritized against other initiatives.
Moreover, a management system for maintaining documentation for the dynamic nature of equipment and piping data needs is usually absent. It is thus, difficult to integrate the RBI into the MOC program.
Conclusion
To carry out RBI, it is required to get all the data from the equipment files. However, typically, the data is not present. To complete the RBI study, suitable assumptions were made.
The commitment of the management and everyone on the RBI team is necessary. If leaders are unwilling to use the results of RBI, then the value of RBI effort will not be realized. Some think that assembling a team and purchasing software is enough to get started with RBI.
Nevertheless this is only one step. However, the approach is complex and requires numerical efforts. This has posed a challenge to its implementation as an efficient software tool or as a plant strategy for an operating company.
Based on RBI, the most popular approach is to use successive inspection results to estimate the trend of corrosion and recommend for inspection plan on similar locations in the production facility. However, in reality, there are inspection uncertainties in interpreting the inspection results and other problems. An RBI approach has an impregnable grip of a quality-based inspection to comply with future aspects and solutions accordingly.
Please contact us for more information and assistance.