An Overview of Radiography Testing (NDT) and Its Importance
- March 16, 2023
- Posted by: Velosi Author
- Categories: Insights, Inspection
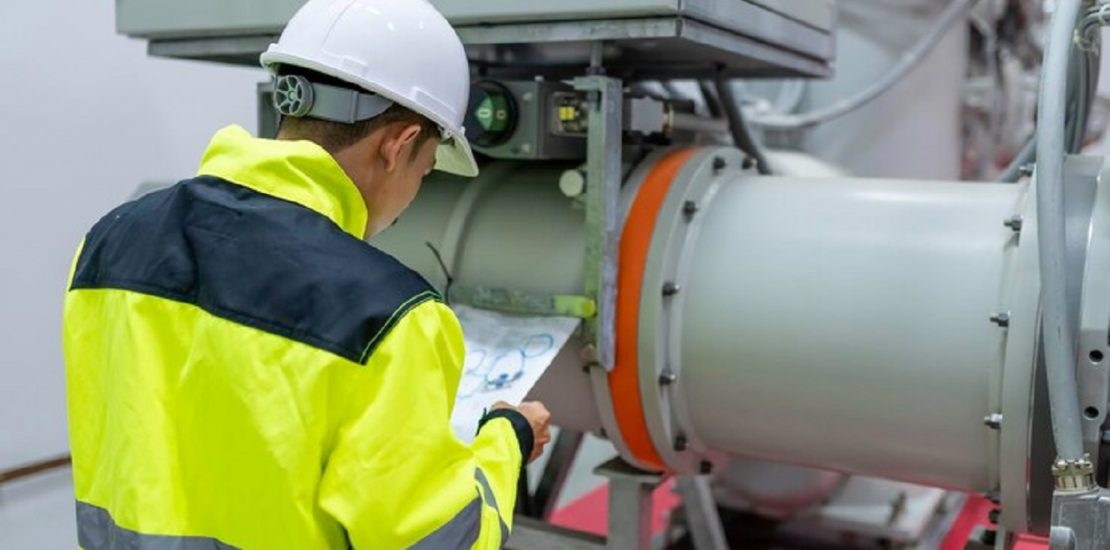
What is Radiography Testing NDT (Non-Destructive Testing) ?
Industrial needs are immensely increasing with time which demands efficient techniques to regulate effective operations. One of the most recognized techniques is NDT (non-destructive testing), used to identify and investigate various materials without causing any damage to them. It is responsible for ensuring the safety of assets and the surrounding.
NDT methods are widely used in the following industries:
- Petrochemical
- Construction
- Manufacturing
- Automotive
- Aerospace
Standard NDT techniques include:
- Radiography testing
- Visual inspection
- Ultrasonic testing
- Liquid penetrant testing
- Magnetic particle testing
Radiography Testing and Its Functionality
Radiography Testing is one of the most common nondestructive testing techniques. It efficiently identifies and evaluates industrial assets for any defects and assists in regulating quality control as well as ensuring safety. It is conducted through an x-ray source machine which captures and reflects radiographic images that are further analyzed to detect any sort of damage or structural defects in the asset.
Defects in materials can occur at any stage and can cause hindrance to ongoing processes, due to which it is critical to test, identify, and evaluate any material defects. In addition, this inspection methodology assists to scrutinize asset structures internally without causing any disruption or damage. Radiography Testing involves quick and efficient imaging procedures with effective response time.
Radiography Testing Functionality involves the following fundamental steps:
- Place the source of X-rays or gamma rays on one side of the material being evaluated.
- Add a detector film on the other side.
- Pass the radiation through the material.
- Evaluate the amount of radiation reaching the detector/film that can be reduced by the material’s density.
- Produce a dark image on the film/detector, as the thicker part of the material absorbs more radiation.
- A resulting image, or radiograph showing an internal overview of the material with any defects such as cracks, or inclusions.
- Examine the radiograph through software to systematically measure any defects.
- Document the measurements taken.
Radiography testing is mainly used in the inspection of welded joints in pipes, pressure vessels, and other structural components, as well as in the inspection of castings, forgings, and other manufactured parts.
Benefits of Radiography Testing
- Precise Detection of Defects
A radiography test is capable of detecting defects within an object’s internal structure. Consequently, this can prevent costly failures and reduce the risk of accidents. In addition to cracks, voids, and inclusions, radiography can detect a range of defects that are not visible to the naked eye.
- Competent and Cost-Effective
There are many benefits to radiography testing, including its efficiency and cost-effectiveness. It can generate detailed images of the internal structure of an object. This streamlined process can save time and money compared to other testing methods, such as destructive testing or visual inspection. It is also possible to automate radiography testing, which further reduces costs and improves efficiency.
- Compliance with Industry Standards and Regulations
Standard and regulatory requirements often require radiography testing. By performing radiography testing, organizations can ensure compliance with safety standards and regulations, which will enhance the quality of assets overall.
- Enhanced Quality Control
Radiography testing can enhance the quality control of products and services. By detecting defects at an earlier stage, organizations can make the necessary adjustments to improve the quality of their assets. Further improving customer satisfaction and asset productivity.
Please contact us for more information and assistance.